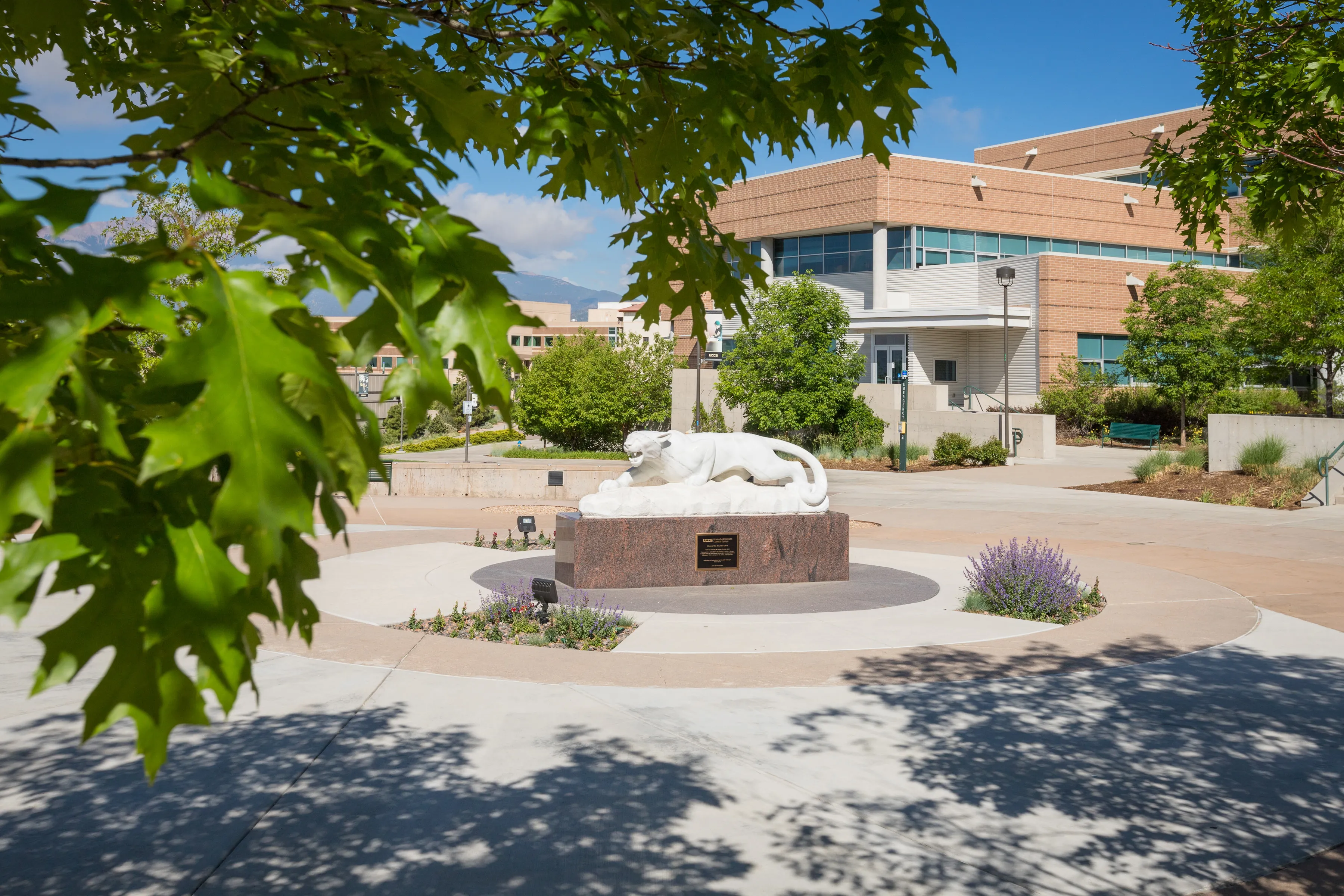
Lab Inspections
Inspections and Corrective Actions
It is the aim of the EHS to work cooperatively with principal investigators and laboratory workers to achieve compliance with University safety policies, the Laboratory Safety Manual and governmental regulations.
Periodically Environmental Health and Safety will conduct inspections of the laboratories on campus. The frequency of the inspections will depend upon the hazards present in each lab, These inspections are not intended to be punitive in nature but rather educational by assisting Principal Investigators to identify areas where they may not be up to standard and assisting them in correcting those areas. A copy of the laboratory inspection sheet is available here (Laboratory Inspection Form)
A report identifying deficiencies and areas for improvement will be directed to the laboratory's Principal Investigator, and any applicable department designee. These items must be corrected within 30 days of receipt of the laboratory inspection report. If the items cannot be corrected in that timeframe, the Principal Investigator must submit a written corrective action plan detailing the expected corrections and estimated date of completion within the same 30 days. The Principal Investigator may designate a responsible party to submit the report. Any inspection finding posing eminent danger (likely to cause a serious hazard, injury, disability or death) must be corrected immediately
In addition to the inspections conducted by EHS, the departmental Chemical Hygiene Officer may also conduct periodic inspections especially during instructional labs to ensure that students are working in a safe environment.
Additional Information
On occasion the University may be visited by federal, state, county or city regulatory inspectors. Some of these groups may contact Environmental Health and Safety (EHS) or the Research Office to initiate an inspection, but others may just present themselves at a lab or building. If this occurs, it is recommended that you follow these procedures:
- Request identification or credentials from the inspector. Write down the inspector's name and affiliation. If satisfactory credentials are not provided, do not offer any further assistance and contact Public Safety x 3111 immediately.
- Contact EHS at x3201 to inform them of the inspection. Provide the affiliation of the inspector when calling to assure the proper response from EHS.
- As per your lab or department's policy, contact your PI, department chair and/or building manager to inform them of the inspector's presence. The department chair and the director of EHS should advise the administration that the inspector is on site and arrange for any close-out conferences requested.
- Do not decline the inspection, however ask the inspector if they can wait until one or more of the above individuals can join the inspection. At a minimum, the PI or EHS representative should be present before proceeding. If EHS is not present before the inspection starts, please take notes of what is said and/or visited until they arrive.
- Answer the inspector's questions, but only provide the information or files that are specifically requested. Do not volunteer information. If the inspector asks to take pictures, do not allow it unless you are able to also take the same pictures for the university's records or verify that they will make them available to the university as well.
- The inspector's status does not authorize him/her to handle any hazardous material in your facility so do not permit this.
- The inspector must always be accompanied by you or other University personnel during the inspection so do not allow them unescorted access to your facility.
- Assure that the inspector wears all appropriate or required personal protective equipment.
If you are contacted to schedule an inspection, please inform EHS and allow the appropriate personnel to be present to assist with the inspection.
If you have any questions regarding these procedures, please contact EHS at x3201 or x3212
You can also checkout the SOP - Surviving an Inspection
EHS routinely checks some emergency equipment such as fire extinguishers, emergency showers, eye wash stations and AEDs. Principal Investigators are responsible for ensuring that first aid, spill equipment and appropriate PPE are available in their laboratories.
In addition, PI's or lab coordinators are responsible for the periodic (preferably weekly) functional testing of eye wash stations.
Eyewash Functional Inspection Log
Note: Emergency showers and eyewash stations are not substitutes for eye and face protection and protective clothing.
Where do I need an emergency eyewash and/or shower?
- In areas where open containers of caustic/corrosive and hazardous chemicals are used (eyewash station and shower).
- Chemical, biological, and radioactive laboratories (eyewash station and shower).
- Shops: at a minimum, eyewash stations are recommended. If hazardous chemicals are used in the shop, a safety shower should also be present.
What kind of eyewash station and emergency shower do I need?
- A hands free unit capable of providing 15 minutes continuous flow at 0.4 gallons per minute for eyewash stations and 30 gallons per minute for showers.
- Hand-held drench hoses may be used in conjunction with safety showers and eyewash stations, but are not a substitute.
Where should they be located?
- Eyewash stations and emergency showers should be located within 10 seconds unobstructed travel (do not block) of the hazard; preferably in the laboratory, shop or work area; and preferably within 10 feet of the hazard.
- What are the testing and maintenance requirements?
- Test the eyewash station weekly to verify proper operation and to flush the line. EHS will flush the emergency showers annually.
Who must be trained to use emergency showers and eyewash stations?
- PRIOR TO USING CHEMICALS IN THE FACILITY ALL EMPLOYEES AND STUDENTS WHO MIGHT BE EXPOSED TO A CHEMICAL SPLASH MUST BE INSTRUCTED IN THE PROPER USE OF THE EYEWASH AND SHOWER.